When a set of coils are requested, the user works out what size of coil is preferred, along with a value of field strength. This then gets worked with between the user, the Electronics technician and the workshop to accommodate other factors such as power dissipation, current and voltage ratings of the wire, mounting points to the bench or feet, and connections from the coils to the controller.
Some coils that are made need to have water cooling, instead of just air cooling. This can be achieved through either mains water or through a water cooling unit. Both types are machinable, assuming that the overall coil size does not hinder this. The units that need extra cooling typically have the coils glued together to improve the heat conductivity from the centre of the coil out. This takes more time, as the glue needs time to set.
Once this is all decided upon, the workshop manufactures the former, ensures it fits the size specification, and sends it through to the coil winder. They then wind the wire onto the former creating the coil. In some cases, there needs to be an additional piece of material made to hold the former onto the coil winding machine. This adaptor is normally a piece of scrap metal or wood, whatever comes to hand. Whilst it is being wound, it will have any thermal glue (if needed) applied, and allowed to set before continuing, If the coils are attached to each other such as in a helmholtz setup, they may be sent back to the workshop for joining together. At the same time that the workshop is making their parts, someone makes the power supply up (with suitable control and ratings) before being attached to the completed coils and checking that the field strength is either within the pre-specified tolerance or able to be controlled over the complete range requested. At this point, the display (if required) is calibrated using a standard tester.
At times, groups have wished to run a double bluff setup on their coils. What they wish to do is have no field produced, or no extra field, yet still have the wires running as normal, and the current flowing as normal so that the operator of the experiment is none the wiser (assuming they don't have a gauss metre to hand). This is achieved by having 2 sets of coils wound onto the same former, and then either in an extra box before the controller or hidden in the main controller box a switch or different wiring configurations to allow the full current of the driver to flow through the coil, but either have full field, or no field present.
Most coil produced sets are between 20mm and 200mm diameter due to the ease of handling within the lab, however we have produced 1 low power set that was ~2m diameter.
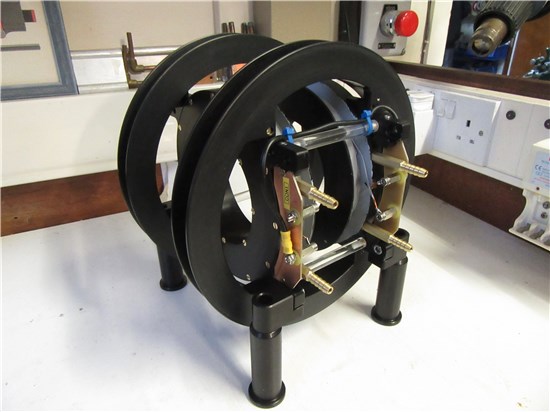
For more coils and past examples see the Helmholtz page under 'past jobs'.